Principal Features of the Metal Magnetic Memory Method and Inspection Tools
as Compared to Known Magnetic NDT methods
Dr., Professor A.A. Dubov
In connection with arising hitherto questions and doubts on novelty of the
metal magnetic memory method (MMM) as compared to known (in Russia and other
countries) magnetic NDT methods, it became necessary to describe once more
principal features of MMM and the appropriate inspection tools.
Methods and tools, used in 70-80 years of the last century at the Institute
of Metals Physics (Sverdlovsk), the Institute of Applied Physics (Minsk),
F.Ferster Institute (Germany) and other Research Centers, were aimed at
measurement of residual magnetization of products after their premagnetization
(and in many cases after their preliminary demagnetization with further
magnetization). Natural magnetization of products (or metal magnetic memory)
used in the metal magnetic memory method was not studied here and was taken as
an interference at measurements.
We established this fact and confirmed it by examination at ROSPATENT while
registering first patents on the metal magnetic memory method. Besides, basic
MMM features were revealed during experimental works at Mosenergo’s power plants
in the course of researches of tubes. Scientific report of the Institute of
Metals Physics (Sverdlovsk, 1988) and monograph [1] contain these basic
features.
The concept of "Metal Magnetic Memory" was first introduced by the author in
1994. Before that time it was not used in the technical literature. The
following terms and concepts were known: "Magnetic Memory of the Earth" - in
archeological studies; "Magnetic Memory" - in sound recording; "Shape Memory
Effect", due to structural and phase transformations oriented by internal
stresses in metal products.
Based on the established correlation of dislocation processes with the
magnetic phenomena physics, the concept of "metal magnetic memory" was
introduced in products’ metals and a new method of diagnostics was developed.
The uniqueness of the metal magnetic memory method is that it is based on use of
the self-magnetic leakage field (SMLF), occurring in zones of steady strips of
dislocations sliding, stipulated by working loads action. SMLF occur because of
domain boundaries formation at accumulations of high-density dislocations
(dislocation walls). It is impossible to obtain an information source like a
self-magnetic field at any conditions with artificial magnetization in working
constructions. Such information is formed and can be obtained only in a weak
external field, as the Earth’s magnetic field is, in loaded constructions when
deformation energy is a cut above the energy of the external magnetic field. It
is shown in practical works that MMM can be used both at the equipment operation
and after working loads relief during the repairs. Magnetic texture, formed
under the action of working loads, becomes, so to say, "frozen" after unloading
by virtue of the "magnetic dislocation hysteresis". Thus, there appears a unique
possibility to evaluate the actual stress-strained state of the equipment and to
reveal at an early stage maximal damage zones in metal by reading this
information using special tools.
Physical fundamentals of SMLF occurrence are principally different compared
to magnetic leakage fields (MLF) occurring on defects of products at their
artificial magnetization used in well-known magnetic NDT methods. SMLF occurs in
local zones (from 0,1 up to tens of microns) on the surface and in depth layers
of products metal. Nobody has never performed investigation of SMLF and the
physical fundamentals of its occurrence till "birth" of MMM (the 90-s of the
last century). There was no such task at all! [2, 3] gives more detailed
description of the mechanism of SMLF formation in ferromagnetic products.
SMLF was found also on new machine-building products directly after their
manufacturing. It is known that at heating of a ferromagnetic above the Curie
temperature (for example, for iron Тc=780°С) and its further cooling even in a
weak external magnetic field of the Earth, it gains such a degree of
magnetization that can be reached at normal temperature only in a high-intensity
magnetic field. Natural magnetization at manufacturing of machine-building
products forms, as a rule, exactly at such conditions. The mechanism of the
product’s real magnetic texture formation (fusing, forging, thermal treatment,
welding) occurs directly after crystallization at cooling below the Curie point.
Here the process of real products cooling is, as a rule, non-uniform. The metal
external layers cool faster than the internal ones. Thermal stresses form across
the product’s volume. They form the lattice and the appropriate magnetic
texture. In areas of the greatest lattice defects concentration (i.e., clusters
of dislocations) and of the structural non-uniformity the domain boundaries (DB)
attachment points form with outcrop in the form of the lines of SMLF normal
component’s sign changing (Нр=0
lines). It was established in industrial researches that natural magnetization,
formed in such a way, reflects the product’s structural and technological
heredity, and Нр=0 lines
correspond to the lines of residual stresses concentration. A series of methods
on quality control of machine-building products using MMM was developed.
Special scanning devices including not only the known flux-gate sensors but
also the length meter, analog-digital converter (ADC), the processor and other
devices were first developed to register local micron SMLF areas giving MMM
characteristic of the stress concentration zone. Such scanning devices have
never been used in magnetic NDT methods before the MMM "birth" (there are no
analogues in the world). Scanning devices and the control method are patented in
Russia, Germany and Poland.
It is known that development of tools providing the opportunity to perform
any researches with enlarged sensitivity or precision as compared to the
existing ones results, as a rule, in big achievements in this or that branch of
science and technology. When we manage to create tools with special, principally
new qualities, providing the possibility of reliable registration of changes in
physical processes that were elusive before, i.e. allowing to bring to practice
tools with completely different performance capabilities, it always leads to
discoveries representing the breakthrough in the most important areas of our
natural knowledge.
This exactly happened to information provided by the construction or product
itself in the form of SMLF. It is principally impossible to register
regularities in SMLF distribution on test objects without special scanning
devices, transformers and program-controlled processors used in tools for MMM.
Before the MMM "birth" generic the residual magnetization field of products was
considered as an interference, and in many cases actions were taken to eliminate
this, so to say, random magnetization.
At operation most of metal constructions work in conditions of cycling loads
and stresses Δσ action and in presence of the external magnetic field Нo (for example, Earth’s field). Due to the known magneto-elastic
effect, "self-magnetization" of equipment and constructions occurs. Figure 1
shows the magneto-elastic effect action diagram. Equipment and constructions
"self-magnetization" phenomenon is being fought against everywhere by their
periodic demagnetization (shipbuilding, power engineering, ball-bearing and
other industries). Upon studying of this phenomenon on the example of boiler
tubes and other units operation, the author offered for the first time to use it
for the purposes of technical diagnostics [1, 4].
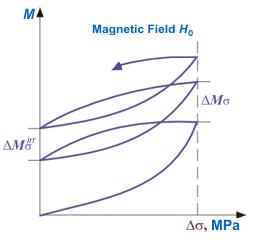
Fig.1. The diagram of magneto-elastic effect
action: ΔМσ and ΔМσirr - change of
residual magnetization, accordingly, under loading and after unloading; Δσ -
change of cyclic loading; Н0 -
external magnetic field.
ММM has been developed in practical and theoretical aspects for more than 25
years. As of 2008, there are more than 40 guiding documents and methods agreed
with RF State Engineering Supervision (Rostechnadzor) and being valid for
various industries.
Special inspection instruments and the appropriate software for them was
developed and put to full-scale production by Energodiagnostika Co. Ltd. The
instruments are certificated in Gosstandard of Russia and are included in the
State List of Measuring Instruments. Certificates RU.C.34.003.A No.22257 and
No.22258.
Since 1996 the Russian and International Centre for experts training and
certification by the method of metal magnetic memory with issuing of Level I and
II Certificates operates in Moscow. The branches of the centre operate in Warsaw
and Beijing. As of 2008, more than 1300 experts in Russia, more than 250 experts
in China and 70 experts in Poland passed training.
Three standards of Russia are approved:
-
GOST R 52005-2003. Nondestructive testing. Method of metal magnetic memory.
General requirements.
-
GOST R 52081-2003. Nondestructive testing. Method of metal magnetic memory.
The terms and definitions.
-
GOST R 52330-2005. Non-destructive testing. Stressed-strained state test on
industrial objects and transport. General requirements.
-
The standard of the Russian Welding Society ST RWS 004-03 "Nondestructive
testing. Welded joints of equipment and constructions. Method of metal
magnetic memory"
16 terms and definitions reflecting the novelty and features distinguishing
MMM from all other known magnetic NDT methods were brought to effect by GOST R
52081-2003.
Interest of experts of Russia and other countries from various industries to
essentially new magnetic method of non-destructive testing (NDT) grows steadily.
Application of the MMM method and corresponding inspection devices to industry,
as a rule, is carried out on a voluntary basis that is vivid confirmation of the
method efficiency.
The metal magnetic memory method and appropriate testing instruments are used
at more than 1000 Russian enterprises. Besides Russia, the method was
implemented at a number of enterprises of 25 countries: Argentina, Angola,
Australia, Bulgaria, Byelorussia, Canada, China, Finland, Germany, India, Iraq,
Iran, Israel, Kazakhstan, Latvia, Lithuania, Macedonia, Moldova, Mongolia,
Montenegro, Poland, Serbia, South Korea, Ukraine, USA.
Interest to the method is caused by unsolved problems, which arise in
practice at quality control of engineering products, at reliability control and
at equipment life estimation.
Let’s denote the basic from them.
-
Till now on the majority of manufacturing plants in Russia and other
countries there are no 100% quality control of production on heterogeneity of
metal structure. Due to this reason the spread of mechanical properties on new
products reaches 20% and more, that considerably reduces their lifetime.
-
Welding exists more than 100 years, and NDT methods, which allow in
practice to carry out express quality control of welded joints in the united
complex system of the factors "structural-mechanical inhomogeneity – defects
of a weld – structural and technological stress concentrator", till now are
not present. Now non-destructive test is commonly applied with detection of
inadmissible defects (at that, the scientifically-grounded norms for the sizes
of permissible defects in welded joints from the point of view of fracture
mechanics, as a rule, are not present). The most important – distribution of
the residual welding stresses determining welded joint reliability till now is
not examined.
-
Existing problems of a lifetime estimation of the aging equipment with
usage of conventional methods and control devices are not solved because of
their unfitness for early diagnostics of fatigue damages.
It is possible to speak confidently, that if we have the old equipment, which
we cannot 100% inspect on metal structural damaging and detect imminent damages;
in this case we work on sudden failure.
Thus, in spite of the fact that nondestructive testing exists in Russia and
other countries already more than 100 years, many problems of machine-building
products quality control and diagnostics of equipment in service are still
unsolved. Therefore demand of the MMM method directed on the solution of
specified NDT problems, is caused by daily practice and a life of the
enterprises.
The metal magnetic memory method by its contents and physical essence
(principally different physical field - SMLF - is measured) represents not only
the principally new magnetic NDT method, but it also opens a new direction in
technical diagnostics as it combines potential opportunities of NDT, fracture
mechanics and metal science.
From the viewpoint of tasks solved by MMM, this method, similarly to the
acoustic emission method, shall be referred to as a method of early diagnostics
of the equipment fatigue damages, and it is feasible to found a Special Advisory
Committee at the RF State Engineering Supervision (Gosgortechnadzor) to consider
this item. Taking into account the current availability of all
standard-technical documentation, a training center ("Energodiagnostika")
independent body for personnel certification) and certified inspection tools, it
is feasible to include this method in the State Engineering Supervision’s system
of non-destructive testing as a separate type of NDT.
Reference
1. Dubov A.A. Diagnostics of boiler tubes with usage of
metal magnetic memory. Moscow: Energoatomizdat, 1995. 112p.
2. Vlasov V.T., Dubov A.A. Physical bases of the metal
magnetic memory method. Moscow: ZAO "TISSO", 2004, 389p.
3. Dubov A.A., Dubov Al.A., Kolokolnikov S.M. Method of
metal magnetic memory and inspection devices. Training handbook. Moscow: ZAO
"TISSO", 2008. 365p.
4. Dubov A.A. Method of definition of service durability of
pipes of ferromagnetic materials. Inventors certificate 1769105. The patent of
Russia // The bulletin of the inventions, No.38, 1992. |