Gas and oil pipelines residual life assessment based on modern methods of
engineering diagnostics
Dr., Professor A.A. Dubov (Energodiagnostika Co. Ltd), I.I. Veliulin
(VNIIGAZ Co. Ltd)
Ageing of oil- and gas-trunk pipelines places the task of their functioning
safety and reliability assurance in the list of the most important state
problems. The suggested complex diagnostics is based on assessment of the real
lifetime: it most optimally combines the operational experience and the early
diagnostics of future damages. Timely replacement of segments with stress
concentration zones (5-10% of the entire main length) will allow ensuring the
fail-safety of pipelines operation.
The traditional approach to maintaining pipelines operability by performing
overhauls of individual sections mainly with complete insulation coating and
pipes replacement cannot provide safety and reliability of gas-trunk pipelines
because of their long length and distinctly different state. Therefore operation
and repair "according to the actual state", i.e. shifting to selective "spot"
repairs of elements and sections based on results of a 100% diagnostic
inspection of many-kilometers-long pipelines becomes the main strategy for
providing high reliability of trunk systems.
In order to ensure reliable and safe operation of gas and oil pipelines,
operated for a long time, a concept is proposed, which incorporates the
following stages:
-
Analysis of damages, non-destructive and destructive metal testing and
worn-out sections replacement according to the available statistics of an
operating organization.
-
A 100% inspection of all gas and oil pipeline sections using up-to-date NDT
methods and means (in-pipe diagnostics, non-invasive magnetometric
diagnostics, the metal magnetic memory method, acoustic emission) allowing
carrying out early diagnostics of damages and detecting stress concentration
zones (SCZ), which are the main sources of developing damages.
-
Inspection with traditional NDT means (USD, X-ray, metal mechanical
properties and structure investigations) is performed on gas and oil pipelines
with detected SCZ after the "prospecting" operation.
-
A 100% diagnostics of pipes using the scanning devices and
instrument-computer complexes, making it possible to carry out the pipes’
state assessment and sorting in the rapid inspection mode during the planned
replacement of insulation.
-
A 100% fittings examination using the metal magnetic memory method and
other NDT methods.
-
Summarizing the results of a complex 100% inspection and developing of
measures aimed at assuring gas and oil pipelines reliability with making the
schedule of the physically worn-out most susceptible to damaging pipe sections
replacement.
-
Confirmatory strength calculation taking into account the metal damaging
and wear nature of pipelines for certain most stressed sections with SCZ left
in operation.
The proposed concept is based on assessment of the real life of gas and oil
pipelines since such an assessment most optimally combines the operational
experience (former damaging statistics) and the early diagnostics of future
damages using the up-to-date methods.
Energodiagnostika Co. Ltd. has more than 12-year experience of gas and oil
pipelines inspection using the metal magnetic memory (MMM) method, specialized
instruments and scanning devices. This experience is reflected in the Guideline
Document GD 51-1-98 "The technique for on-line diagnostics of local gas and oil
pipeline segments using the metal magnetic memory method". This Guideline
Document was approved in 1998 by "Gazprom" JSC and agreed with the Supervision
Agency in the oil and gas industry of the Russian State Technical Supervision
Bureau (Rostechnadzor).
During the period from 1998 till 2004 the above-mentioned technique and the
appropriate inspection instruments of the type TSC-1M (Tester of Stress
Concentration) were used at a number of "Gazprom" JAC and "Transneft" JSC
enterprises. In particular, the following enterprises should be noted:
Urengoigazprom, Severgazprom, Mostransgaz, Uraltransgaz, Yamburggazdobytscha,
STC Nizhnevartovsk, a number of "Transneft" JSC enterprises and others.
It should be noted that the Russian National Standard GOST R 52005-2003
"Non-destructive testing. Metal magnetic memory method. General requirements" on
the metal magnetic memory (MMM) method was put in effect in 2003.
For on-line inspection of welds and walls of large-diameter (?530÷?1420 mm)
gas and oil pipelines in 2004 Energodiagnostika Co. Ltd. jointly with "VNIIGAZ"
Co. Ltd. developed a scanning flaw detector, allowing carrying out the state
assessment of the entire pipe surface at an average rate of 200 meters per hour
(the scanning rate of 10 meters per minute can be ensured). At that insulation
removal and pipe surface dressing are not required and the natural magnetization
of the metal, formed in the course of operation (the magnetic memory of metal)
is used.
The scanning flaw detector (fig.1) is a device made in the form of two
attached to each other rings, on which there mounted 24 flux-gate transducers,
integrated with the wheels, allowing the operator to move the scanning device
along the pipeline. The operator moves the scanner along the external pipe
surface using the spacer rod. At the same time the operator may be directly on
the pipe or near the pipe (at a distance of 5-6 m), moving on the ground
together with another operator, who watches the inspection results on the screen
of a specialized TSC-type (Tester of Stress Concentration, RF Gosstandard
Certificate RU.C.37.003 A No.9192) instrument. The scanning device can be used
as a set with a laptop-based instrument.
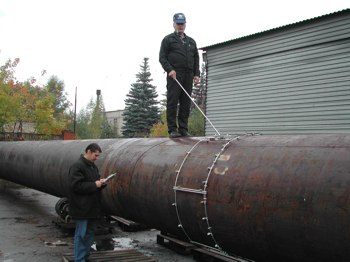
Fig.1. General view of the scanning device
covering the entire diameter of a ?1420 mm pipe with application of the
instrument-computer complex based on the metal magnetic memory method.
For a pipe with the maximum diameter of 1420 mm the distance between the
sensors, arranged along the perimeter, is 180 mm. According to the experience of
such-diameter gas pipelines inspection, the anomalous magnetic field spot in the
area of, for example, a surface stress corrosion crack represents an ellipse
with the large axis length up to 500 mm and the small axis length up to 200 mm.
Presence of 24 sensors (their number may be increased up to 32) allows reliably
covering the entire pipe surface. For smaller-diameter pipes the distance
between the sensors is reduced and, accordingly, the inspection efficiency
increases.
The basic diagnostic parameter during the inspection of the outer surface of
pipes using the MMM method is the gradient dНр/dх of the magnetic field intensity (or
the intensity of its variation) in the zone of stresses and strains
concentration due to the development of various-type defects. While assessing
the state of the pipeline metal, it is necessary to know the limiting field
gradient, corresponding to the ultimate strength of the metal (fig.2). These
limiting values are determined in the course of industrial and laboratory
investigations. From the positions of fracture mechanics, meeting the limiting
state by the metal does not depend on the type of defect causing this state. It
is characterized by the integral diagnostic parameter – the density of the
mechanical and, accordingly, the magnetic energy on the surface and in the
volume of the pipe body [1].
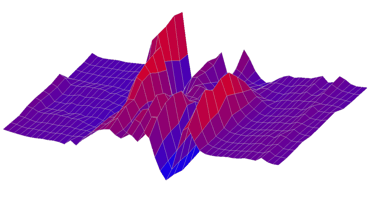
Fig.2. Fragment of the magnetic field Нр distribution on stress corrosion cracks.
The magnetic field gradient, detected automatically in the course of
scanning, is displayed on the instrument screen as columns with binding to the
number of the sensor on the scanning device (see fig.3, a) as soon as
it crosses the defected zone.
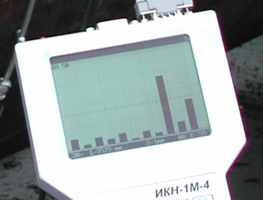 |
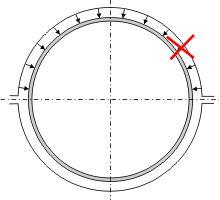 |
Fig.3a. Display of inspection
results on the screen of the instrument when the scanning device moves
along the pipe surface. |
Fig.3b. Marking of the
defected zone in the pipe logbook. |
When the limiting field gradient, which is preliminarily set up during the
instrument adjustment, is exceeded along any of the measurement channels, the
operator stops, records this area to the instrument’s memory and tells another
operator to put a corresponding mark on the logbook or directly on the pipe
surface (see fig.3, b).
The Methodical Guideline (MG) on carrying out the inspection of
large-diameter (?530÷?1420mm) pipelines using the specialized scanning devices
were developed. This MG specifies the limiting field gradients for the above
mentioned diameters of pipes. These gradients characterize the limiting state of
the metal by the strength conditions, as well as the initial development of
cracks.
The existing experience in inspection using the metal magnetic memory method,
the TSC-type instruments and the scanning devices, which do not require any pipe
surface preparation, demonstrates the following: pipes, located on the same gas
pipeline segment and being in the long-time operation under identical
conditions, are in a distinctly different state. If in the course of the
inspection no magnetic anomalies are displayed on the screen, it indicates that
the pipe metal’s state is satisfactory and there are no developing defects on
it. At that the inspection speed is not higher than 2 min per 10 m of the pipe
length. In case the zones with the magnetic field gradient value higher than the
limiting values are detected, all these zones are marked in the pipe logbook
according to the described above technique. Then the qualifying inspection using
the eddy-current instruments and UFD is carried out in these zones.
It is appropriate to carry out the described above diagnostics of pipes using
the scanning devices in the field or factory conditions during the planned
replacement of insulation, on open above-ground pipeline segments, during
grading of used pipes, as well as before laying of new pipes into trenches.
In order to solve the problem of a 100% inspection of gas and oil pipelines
non-invasive magnetometric diagnostics (NIMD), allowing determining the most
stressed pipe segments located at the soil depth of 2 m and deeper without
artificial magnetization and changing of operating mode, has been developed
during the recent years.
Experimental samples of "IAM" instrumentation (development of VNIIGAZ and
"Gazpribortechnologia-M" LLC), "MBS" series "SKIF" instruments (development of
"Transkor-K" SRC, TSC-3M instruments (development of "Energodiagnostika" LLC)
passed route survey and demonstrated their effectiveness. The appropriate
reference-legal documents (on NIMD technology of NDT performing) [2, 3] are
known.
Energodiagnostika Co. Ltd. developed a measuring complex for NIMD of gas and
oil pipelines, located at the soil depth of 2 m and deeper. When the operator
moves along the route at a speed of not less than 2 km per hour, the segments
operating in the most stressed conditions and being susceptible to damaging are
detected. Prospecting and additional inspection are carried out on these
segments in order to detect specific defects.
NIMD is based on measurement of the magnetic field of the earth (Нe) distortions due to changing of the pipe
metal’s magnetic permeability in SCZ and in the corrosion-fatigue damaging
development zones. The nature of the field Нe variation (frequency, amplitude) is
conditioned by the pipeline strain occurring in it due to the influence of a
number of factors: residual process and installation stresses, the working load
and self-compensation stresses at outdoor air and environment (soil, water,
etc.) temperature fluctuation.
The local variation of the magnetic field by all the three components with
the maximum value of the field’s gradient (see the bottom part of the
magnetogram in fig.4) takes place in the zone of the assumed stress
concentration. The inspection was carried out using the magnetometric tester of
stress concentration (TSC-3М) and the specialized highly sensitive sensors
manufactured by Energodiagnostika Co. Ltd.
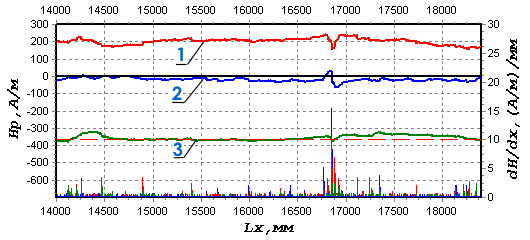
Fig.4. Fragment of the Нр magnetic field distribution in the stress concentration
zone on a buried gas pipeline segment (?530mm, St.20): 1 - the horizontal
component of the Нр field along the pipe axis; 2 - the
horizontal component of the Hp field across the pipe axis; 3
- the normal (vertical) component of the Hp field.
The criteria developed based on the 20-year experience of the use of the
metal magnetic memory method directly during the inspection of pipelines are
used at magnetograms decoding and classification of magnetic anomalies. A
program software "MMM-System" is used for processing of the results and
detecting of the segments operating in the most stressed conditions.
The Methodical Guideline (MG) for carrying out the non-invasive magnetometric
diagnostics of gas and oil pipelines using the TSC-2M-8 and TSC-3M-12 type
instruments was developed. The proposed MG contains the description of the NIMD
principle, which allows detecting and localizing the stress-strain states, as
well as detecting the presence of various-nature damages in the metal of buried
and under-water pipelines and of the pipelines exposed to other
environments.
The experience of the practical application of the measuring complex with
confirmation of the inspection results directly on the pipe after carrying out
prospecting ensures that NIMD is efficient "in the hands" of well-trained
experts. At present experts in the metal magnetic memory method and NIMD are
trained at Energodiagnostika Training Center (Moscow).
Bibliography
1. Vlasov V.T., Dubov A.A. Physical Bases of the Metal
Magnetic Memory Method. Moscow: ZAO "TISSO", 2004. 424 p.
2. GD 12-411-01. The instruction for technical state
diagnostics of buried steel gas pipelines. Moscow: STC "Promyshlennaya
Bezopasnost", 2002.
3. GD 102-008-2002. The instruction for technical state
diagnostics of pipelines by the non-invasive magnetometric method. Moscow:
"VNIIST" JSC, 2003. |