The metal magnetic memory method
Dr., Professor A.A. Dubov
For the first time the author introduced the concept "the magnetic memory of
metal" in 1994. Before that this concept was not used in the technical
literature. The following terms and concepts were known: "the magnetic memory of
the earth" in archeological investigations, "the magnetic memory" in sound
recording and "the effect of shape memory" conditioned by the oriented internal
stresses in metal products.
Based on the established correlation of dislocation processes with the
physics of magnetic phenomena in the metal of products, the concept "the
magnetic memory of metal" was introduced and a new diagnostic method was
developed. Similar to the effect of shape memory, "the magnetic memory of metal"
- is the effect of the magnetic memory of metal strain conditioned by the
oriented internal stresses. The uniqueness of the metal magnetic memory (MMM)
method consists in the fact that it is based on application of the effect of
occurrence of high metal magnetization in the areas of large strains of
structural elements’ metal due to the exposure to working loads. At the same
time there is no artificial source of magnetization, except for the weak
magnetic field of the earth, in which we all exist.
Many of us also observed the effects of occurrence of high metal
magnetization, for example, in case of cutting of some metallic product with a
hack-saw, or at the end of the screwdriver after its influence on the screws, as
well as in places of friction at contact of metallic products (for instance, of
gear wheel teeth). Occurrence of anomalous magnetization can be observed on the
metallic wire in the area of its cyclic strain. When we break the wire by its
cyclic bending in different directions, our fingers feel the wire heating in the
maximum strain site. And if we carry out some measurement in this place using a
magnetometer, we shall record the increase of the metal’s magnetization.
Oscillation damping – absorption of the energy of mechanical oscillations (for
example, of turbine blades) is accompanied by generation of the magnetic energy
and, accordingly, by the growth of the metal’s residual magnetization. The list
of the observed in practice cases of the products metal magnetization without
the source of the artificial magnetic field can be continued further.
The phenomenon of strong magnetization of boiler pipes metal in places of
their damaging, discovered in the 70-s of the last century by the Chief of
"Volgogradenergo" metals laboratory O.V. Philimonov, should be attributed to the
history of occurrence and development of the metal magnetic memory method as a
new direction in diagnostics. The discovered phenomenon roused the interest of
many power engineering experts, including me. At that time I worked for the
production service of "Mosenergo" and dealt with the problems of boiler pipes
reliability assurance. At that time an assumption was made about the possibility
to use the phenomenon of operated pipes self-magnetization in order to detect
potential damages. And occurrence of high magnetization was presumably explained
by the action of cyclic strains and stresses due to working loads.
In case of confirmation of this assumption there opened a unique possibility
to detect by the residual magnetization of metal in the location of stress
concentration - the source of damages occurrence and development - by means of
readout of the magnetic information presented to the researcher by the boiler
piping itself.
In connection with this circumstance the author of this paper, jointly with
the experts of the Institute of Metals Physics of the Russian Academy of
Sciences (Yekaterinburg), arranged and carried out special laboratory and
industrial researches aimed at investigation of the phenomenon of boiler pipes
magnetization in conditions of their operation. The results of these
investigations are described in the dissertation and monograph by A.A. Dubov
"Diagnostics of boiler pipes using the magnetic memory of metal" (Moscow:
Energoatomizdat, 1995, 112 p.).
As a result of the carried out investigations it was demonstrated that the
reason of anomalously high magnetization of individual segments of boiler pipes
is the magnetoelastic effect, which is known in the physics of magnetic
phenomena.
Fig.1 shows the scheme of appearance of the magnetoelastic effect causing the
growth of residual magnetization (М), for instance, in any place of the
structure there is a cyclic load Δσ and an external magnetic field Н0 (for
example, the field of the earth), then the residual magnetization ΔМσ
growth takes place in this location. Upon the load relief the reversible
component disappears, and only the irreversible component of the residual
magnetization (ΔМσirr) remains. Due to the
magnetoelastic effect the pipes are as though "self-magnetizing" in the zones of
stress concentration due to working loads. In the course of further industrial
investigations it was established that practically all units of metal components
and structures are subject to "self-magnetization".
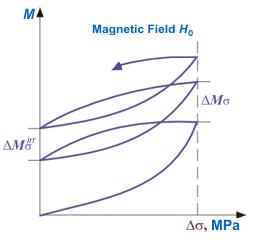
Fig.1.
The phenomenon metal components and structures "self-magnetization" is fought
against everywhere by means of their periodic demagnetization (shipbuilding,
power engineering, ball bearing and other industries). It would be sufficient to
give as an example of struggle against self-magnetization, as a "harmful"
phenomenon, the well-known story of struggle against the mines combated by our
scientists at the beginning of the World War II against Germany. At that time,
for example, occurrence of strong magnetization of hulls was discovered due to
impacts of waves, especially after the storm. And then this phenomenon of hulls
magnetization under exposure to cyclic stresses due to wave impacts in
conditions of the weak magnetic field of the earth was first investigated under
the supervision of academician A.P. Alexandrov. This phenomenon was explained by
the action of the magnetoelastic effect. Then, in order to fight against the
magnetic mines, special demagnetizing devices for periodic demagnetization of
hulls were developed.
Since then the natural phenomenon of metal components and structures
"self-magnetization" is everywhere fought against by means of their periodic
demagnetization.
Upon investigating of this phenomenon on the example of boiler pipes and
other units, it was suggested for the first time to use it for the purposes of
engineering diagnostics, and the new diagnostic method was called "the metal
magnetic memory method".
Based on experimental investigation of the metal magnetic memory phenomenon,
a number of practical inspection techniques and specialized modern instruments
were developed, allowing registration of magnetic anomalies location sites,
corresponding to stress concentration zones (SCZs), being the sources of
damages, in the quick-inspection mode without any preparation of the inspection
object (IO) (in some cases through the layer of paint or insulation) by scanning
along the surface (for example, of a long pipeline). Obtaining such an
information source like a proper magnetic field is not possible under any
conditions of artificial active magnetization in operated structures. Such
information is formed and can be obtained only in a weak external field like the
magnetic field of the earth in loaded structures, when the strain energy exceeds
the external magnetic field energy by at least an order of magnitude. It was
demonstrated in practical investigations that MMM may be applied both for
equipment operation (in the monitoring mode) and after relief of working loads,
during the repairs. By virtue of "magnetodislocation hysteresis" the magnetic
texture formed under the effect of working loads somehow "congeals" after their
relief. Thus, there is a unique opportunity to perform assessment of equipment
stress-strain state and detect zones of maximum metal damage by measuring this
information using specialized instruments. Application of MMM for assessment of
metal structural life and survivability looks very promising since this method
unites potential opportunities of non-destructive testing, materials science and
fracture mechanics.
The unique opportunities of the MMM method reveal themselves in cases of
finding out the reasons of failure of various structural elements of buildings,
constructions, bridges, etc. For example, at failure of one of the piers
supporting the roof in aqua park (Moscow, 2005) or at failure of the so-called
"finger" carrying the heavy load in a complex structure of the new skating rink
building (Moscow, 2007), the arouse some arguments between the metallographers
(and, accordingly, between the manufacturing plant) and the designers of these
structures. In these cases it is impossible to assess the actual stress-strain
state (SSS) using the design methods with application of current design norms
and relying on the theory of metals’ resistance, which does not take into
account the structure inhomogeneity. If in these cases of occurred failures of
structures (and best of all – not waiting for failure to occur) there was a
possibility of their inspection using the MMM method and the appropriate
scanning devices, then it would be possible to assess the actual SSS of any
structural element by the diagram of the self-magnetic field distribution. SSS
assessment using the MMM method has an integral nature, taking into account all
the factors: design peculiarities, structural inhomogeneity of each element,
factory, installation and operational factors. Now the designer has the
opportunity to see the work of his "brainchild".
Due to the use of the metal magnetic memory effect during the diagnostics of
metal components and structures it became possible to fulfill many problem
tasks. First of all, this is prediction of metal components’ reliability and
lifetime. Based on the 100% inspection of structures, the MMM method and the
appropriate instruments allow detecting all potentially dangerous areas (SCZs)
and revealing the reasons for their occurrence. Using the program software,
these zones are classified by the degree of their danger. It allows timely
conducting the repairs or replacement of individual elements and granted
prolongation of the IO’s lifetime, at least till the next overhaul and/or
inspection.
Welding exists in the world for more than 100 years, and the most important
factor determining reliability of a welded joint - distribution of residual
welding stresses - is so far not controlled due to the lack of NDT methods
suitable for wide practical application. The use of the metal magnetic memory
effect allows solving this problem. Reading out of the residual magnetization,
formed naturally during welding with subsequent metal cooling, provides a unique
possibility to integrally assess the actual weld state: to detect welding
defects simultaneously with the distribution residual welding stresses.
Formation of the magnetic (domain) texture in welded joints occurs
simultaneously with crystallization during metal cooling in the weak magnetic
field of the earth (or of the workshop) and its passing through the well-known
Curie point (760-770°С for carbon steel grades). In conditions, when the energy
of thermal strains and stresses is by order higher than that of the weak
magnetic field, the residual magnetization distribution in the weld metal is
conditioned by the appropriate distribution of residual stresses (RS).
An amazing fact! The physical Curie point (Pc) and the effects of magnetization
disappearance, when the metal is heated above the Pc and, on the contrary, of high magnetization
appearance when the metal is cooled below the Pc have been known to experts as far back as since
1895, when the French scientist Pierre Curie first discovered this physical
effect. However till date this effect has not been used in the everyday
practice, for example, for quality assessment of products at engineering
plants.
In the course of industrial investigations we established that the magnetic
memory of metal on ferromagnetic products (and in some cases on the products
made of a paramagnetic material) reflects their structure and process history.
During fabrication of any products (melting, forging, punching, heat treatment,
welding) when they are cooled below the Pc in a weak magnetic field of the earth (or of
the workshop) the magnetic texture is formed naturally. Upon studying the
distribution of the natural magnetization on a large number of new products
after various technological processes at manufacturing plants, a number of
practical techniques for inspection of the products’ quality was developed. And
the unique possibilities of the metal magnetic memory application for testing of
the effectiveness of products manufacturing technologies (quality inspection of
casting, heat treatments, etc.) were revealed.
It should be noted that nowadays there is no 100% quality inspection of
products for structural inhomogeneity at engineering plants both in Russia and
abroad. According to the statistics, it is known that approximately up to 20% of
the new products (pipes, rails, shafts, etc.) are put in operation with
unacceptable metal defects. Application of the metal magnetic memory effect
during the quality inspection of products at the manufacturing plants will allow
carrying out rapid sorting of products and not to let the products with metal
defects and process manufacturing defects be put in operation. Equipment and
instrument-computer complexes using the metal magnetic memory effect during the
inspection are considerably simpler and cheaper as compared to the available
ultrasound-based equipment or equipment using artificial magnetization.
At present the magnetic NDT methods applied at manufacturing plants use
artificial magnetization of products. At that the natural magnetization (the
magnetic memory of metal – the most valuable information!) is removed by means
of preliminary demagnetization.
What keeps from wider implementation in practice of the new direction in the
engineering diagnostics based on the use of the metal magnetic memory effect
today? Here it is appropriate to quote the words of the German poet and thinker
Johann Goethe (28.08.1749 – 22.03.1832): "If somebody points out
something new … people reject it as hard as they can; they behave as if they do
not hear or cannot understand, speaking about the new opinion with contempt, as
if it was not worth the effort spent on investigation or attention at all, and,
thus, the new truth has to wait for a long time until it manages to pave its
way".
Appearance of the first publications about the magnetic memory method was at
first met in the scientific circles with indulgent indifference: "mister is a
little bit lost". However further results of original experimental
investigations and practical diagnostics using the MMM method, the quantity and
quality of which grew rapidly, also rapidly gave rise to transition from
indulgent bewilderment to aggressive indignation in the circles of scientists
and experts both in the field of magnetism and diagnostics. And it is no wonder:
many results, obtained using the magnetic memory method, contradicted the
established during many decades’ ideas about magnetism and, first of all, the
concepts like magnetoelasticity and magnetization. Moreover, the necessity to
explain the multiple results of practical diagnostics using the metal magnetic
memory effect revealed the "white spots" existing till date in the theory of
magnetism. As it turned out, the basic provisions of the theory of magnetic
phenomena in ferromagnetic materials were developed in the 30-s - 40-s of the
last century without application of modern conclusions and achievements of
quantum physics and theories of dislocations in the metal.
Consideration of magnetism development in the historical aspect made it
possible to understand that some results could not be used yet and some were
already "rejected" by the theory of magnetism formed.
For these reasons the following questions remained unanswered:
-
what the starting point is and how the process of self-magnetization
develops in the volume of a ferromagnetic;
-
what restricts the domain growth and what its sizes are in absence of
external exposures;
-
what the three-dimensional shape of the domain is, whether its dimensions
are interrelated and if yes, then how;
-
how in conditions of spontaneous self-magnetization the domains form and
group in the volume of a ferromagnetic; whether "closing" domains really exist
as some auxiliary formations;
-
what actually the boundaries between the domains are, since the quantum
physics proved the impossibility of arbitrary spatial position of the atom’s
magnetic moment vector within the lattice. Consequently, the hypothesis about
the gradual smooth turning of the magnetic moment vector in the transition
layer - the interdomain boundary - is wrong;
-
why there is no symmetry in the processes of self-magnetization during
tension and compression of polycrystalline ferromagnetic specimens;
-
why even an ideal monocrystal of a ferromagnetic still initially shows the
magnetic anisotropy;
-
what physically determines the amount of the residual magnetization;
-
what the criterion of magnetic fields division into weak and strong is;
-
whether the magnetic field of the earth influences the process of
self-magnetization;
-
what the influence of weak magnetic fields on the process of magnetization
variation at cyclic loads is;
-
why during the specimens loading their magnetization increases abruptly at
transition to the plastic strain region;
-
how magnetization and the domain structure, determining it, are related to
dislocations and their clusters;
-
why in a loaded ferromagnetic there occur local magnetic fields, the
orientation of which is not related to external magnetic fields, and what
determines their spatial direction;
-
whether the boundary between weak and strong magnetic fields depends on the
state of the environment (of the magnetized material).
Thus, one has to state that, despite the large number of the obtained by the
present time in theoretical and experimental investigations results and
conclusions, developing and supplementing the basic provisions of the domain
structure formation, the theory of the domain structure cannot be considered
completed.
With the purpose of searching for the answers to the formulated question and
explaining the phenomenon of the magnetic memory of metal some theoretical and
experimental investigations were performed. The results of these are reflected
in the book by V.T. Vlasov and A.A. Dubov "Physical bases of the metal magnetic
memory method" (Moscow: ZAO "TISSO", 2004, 424p.).
The carried out investigations resulted in obtaining of the answers to many
above-mentioned questions. It was demonstrated that several physical effects
underlie the phenomenon of the magnetic memory of metal. Besides the known till
date magnetoelastic effect, a new, not studied before effect of
magnetoplasticity - the process of a ferromagnetic object’s self-magnetic field
formation in conditions of plastic strain - was revealed. The direct
experimental proof, confirming the considerable increase of the dislocations
density in stress concentration zones, was obtained during the specimens tensile
testing using the specialized magnetometers and investigation of the dislocation
structure using the electronic microscope. The rules of the magnetomechanical
effect, showing itself at the macro level in the product’s volume, were
investigated.
Based on the analysis of experimental investigations of various industrial
objects using the MMM method and the analysis of the reasons of low
effectiveness of the existing stress control methods, the contradictions between
the diagnostic results and the formed ideas about the characteristics of
internal stresses were revealed.
The bases of the physical theory of the "strain - failure" process were
developed. This theory will ensure objective effectiveness evaluation of various
stress-strained state inspection methods, strength calculations and equipment
life prediction. It will allow providing scientific grounding of defects
admissibility norms and the degree of their hazard in non-destructive testing,
as well as more effective solution of other problems of fracture mechanics.
And, of course, in conclusion it is necessary to quote a well-known phrase:
"Practice is a criterion of truth".
The new direction in engineering diagnostics based on the use of the metal
magnetic memory phenomenon, which was born in Russia, has been developed
practically and theoretically for more than 25 years. The method and the
appropriate inspection instruments are used at more than 1000 enterprises of
Russia. Besides Russia, the method became widespread in 25 countries of the
world.
The inspection technology based on the MMM method was brought to the level of
National and International Standards. In November 2007 International Standards
were published:
-
ISO 24497-1:2007(E). Non-destructive testing. Metal magnetic memory.
Vocabulary.
-
ISO 24497-2:2007(E). Non-destructive testing. Metal magnetic memory.
General requirements.
-
ISO 24497-3:2007(E). Non-destructive testing. Metal magnetic memory.
Inspection of welded joints.
Since 1996 a Certification Center "Energodiagnostika", being an independent
body for personnel certification and conducting training of experts under the
licence of the Russian Technical Supervision Body (Rostechnadzor), has been
operating in Moscow. By the present time about 1300 Russian and more than 300
foreign experts were trained. |