Quality inspection of reconditioning, depositing and spraying
technologies
It is impossible to assure quality inspection of modern reconditioning,
depositing and spraying technologies for worn-out power equipment units and
components without the inspection of the metal’s state before and after the
execution of the above-mentioned technologies. The capabilities of the
conventional methods used for this purpose (selective hardness measurement,
metallographic investigation of the surface layer) cannot ensure the complete
and reliable control of the metal’s state. The problems of metal inspection
occur during the execution of the welding-thermal repair technologies and the
recovery heat treatments (including the high-temperature ones) of welded joints
of collectors, steam pipelines, case-shaped components, drums, rotor blades of
steam turbines and other units.
There is a possibility to solve the above-indicated problem of the metal’s
state control and, accordingly, of the reconditioning technologies quality by
application of the new non-destructive testing method based on the use of the
metal magnetic memory effect.
In the course of industrial and laboratory investigations it was established
that it is unpractical to carry out any type of a reconditioning technology in
presence of irreversible changes in the structure of the repaired unit’s metal,
and if this unit is in the pre-failure state.
The metal magnetic memory (MMM) method, reflecting the product’s structural
and process history, and the appropriate inspection instruments, which do not
require any preparatory works, allow ensuring the 100% quick inspection of the
entire surface and detecting units and components, on which it is unpractical to
execute the reconditioning technology.
Inspection of the metal’s state using the MMM method on power equipment units
and components before and after execution of reconditioning repair technologies
on them allows evaluating the quality of these technologies, the structural
changes, the level and the distribution of the residual stresses.
The techniques and the inspection instruments based on the use of the
magnetic memory of metal are certified in Russia and are in the process of
standardization at ISO. They are available at Energodiagnostika Co. Ltd.
(Moscow).
The similar problem with the residual stress control occurs during carrying
out the repair deposits in crack development zones in various structures.
Fig.1 shows the fragment of the results of the blade #84 inspection by the
MMM method before (fig.1, a) and after (fig.1, b) application
of the wear-resistant coating on the input flange. The powder coating was
carried out in a special furnace at the metal heating to about 300oС.
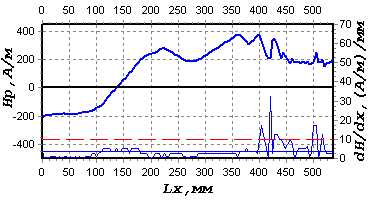
Fig.1a. The results of the blade
inspection before the application of the input flange wear-resistant
coating.
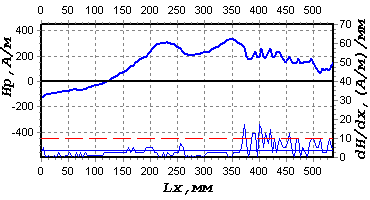
Fig.1b. The results of the blade
inspection after the application of the input flange wear-resistant coating.
It can be seen from the comparison of fig.1, a, and fig.1, b, that in the application area (on the segment from 350 to 550 mm) the
magnetic Hp field and its gradient dHp/dx decreased and
became more uniform. Using the available technique, it is possible to carry out
the quantitative assessment of the reduction level of the radial component of
residual stresses in the deposit area.
Fig.2, a shows the fragment of the results of the Hp magnetic field’s normal component inspection
along the deposited metal in the crack formation area on one of the bridge
construction units. Inspection was carried out according to the arrow indicated
in fig.2, b before treatment with ultrasound (the red graph) and after
treatment (the blue graph). Treatment with ultrasound was performed in order to
reduce the residual stresses in the deposit area.
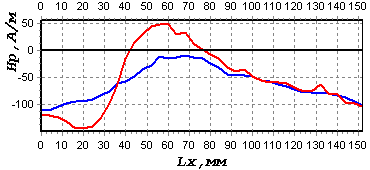 |
 |
Fig.2a. The results of the Hp magnetic field’s normal
component inspection along the deposited metal in the crack formation
area. |
Fig.2b. The scheme of the
deposited metal inspection in the crack formation area: 1 - the
crack. |
It is seen in fig.2, a, that after the ultrasonic treatment the
normal component of the Hp field
and, accordingly, the normal component of the residual stresses decreased, and
their distribution became more uniform. |