Physical criteria of materials' and structural elements' stress-strain state
assessment
Dr. V.T. Vlasov, Dr., Professor A.A. Dubov
Many times we paid attention to the paradoxicality of the situation formed in
solution of the most crucial problem of assessment of structural materials’
stress-strain state and of the residual life of complex technical objects. On
the one hand, the modern diagnostics offers "the entire arsenal" of means for
measuring of materials’ mechanical characteristics, internal stresses and even
the residual, applying various non-destructive physical methods, which quite
complies with the urgency of the problem. And on the other hand, along with the
extremely high demand for the means of assessment of the actually formed state
of the material, practically the complete refusal of fracture mechanics experts
to use the offered means during the residual life determination is observed. And
the motivation of the refusal is quite fair and based on the well-known and
little known objective reasons.
The many-years experimental and practical experience, gained in the course of
the development and practical application of the magnetic memory method during
the diagnostics of various objects, revealed and proved the objectiveness of
"discrepancies" between the actual values of physical internal stress parameters
and the "usual" limiting values of mechanical characteristics, for example, to
the time strength limit.
The results of theoretical investigations of the rules of physical strains
distribution allowed explaining the observed "discrepancies" and proved the
delusiveness of the well-known criterion of the actual material’s state
assessment in local zones of the developing damaging by the degree of closeness
to the reference limiting mechanical characteristics of the material.
In fact, this was known long ago, because by variation of the strained
specimen’s shape we can easily judge about the non-uniformity of the strains
distribution on the specimen (see fig.1). However it did not allow speaking
about the quantitative ratios of strains in different areas of the specimen. We
managed to solve this problem.
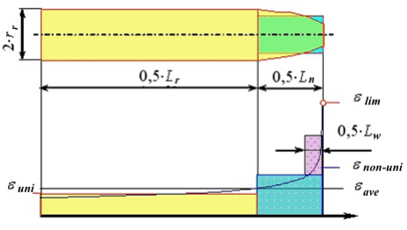
Fig.1. Areas of the uniform and non-uniform
straining and the "neck"of the destroyed specimen: εlim - the limiting strain in
the neck area; εave - the average strain along
the entire specimen length; εuni - uniform straining along
the length Lr ; εnon-uni – non-uniform
straining along the length Ln .
Investigations of the strain-force characteristics of ninety-seven specimens
of various steels and alloys (see table 1) showed that the values of the
limiting external specific forces, reduced to the non-uniform and uniform strain
areas, will notably differ from those for the entire specimen.
Table 1.
No |
Specific features of the group |
Grades of metals and alloys |
Source of parameters |
Number of metals and specimens |
1. |
various steel grades |
st.3; st.6; st.8; st.10; st.15; st.20; st.25; st.30; st.35; st.40;
st.45; st.60; Fe |
reference data |
13 |
2. |
various alloy grades |
Cr13; 20Cr; 38 CrAl; 40Cr; 30CrMo; 34 CrMoAl; 35CrMo; 40CrF; 40CrNi;
1Cr18Ni9Ti; 12Cr1MoF; 15Cr1MoF |
reference data |
12 |
3. |
various alloy grades |
1Cr17Ni2; 12CrNi3Al; 30CrNi3Al; 30CrGSAl; 25Cr2GMoTiAl; 34CrNi3MoAl;
40CrNi3MoAl; 18Cr2Ni4MoAl; 38Cr2MoUAl; 50CrFAl; 60S2 |
reference data |
11 |
4. |
various specimens of the same grade |
Rail steel (for P-50) |
experiment |
27 |
|
|
Aluminum alloy AlMg6 |
experiment |
22 |
|
|
Titanium alloy VTi8 |
experiment |
12 |
|
|
Total |
|
97 |
Fig.2 and 3 show the values of the ratios of the limiting load in the
non-uniform and uniform strain areas to the time strength limit, depending on
the average value of the maximum strain in the non-uniform strain area.
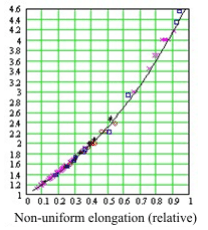 |
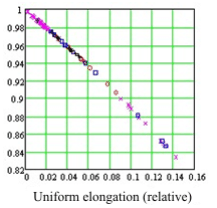 |
Fig.2. The ratios of the limiting
values of the specific load in the non-uniform strain area to the time
strength limit for various materials. |
Fig.3. The ratios of the limiting
values of the specific load in the uniform strain area to the time
strength limit for various materials. |
If we speak about strain during the specimens’ tension, then at time strength
the average strain values in the non-uniform and uniform strain areas differ
even more from the reference values of the material’s relative strains. Fig.4
shows the values of the ratios of average longitudinal strains in the
non-uniform strain area of the specimen to the average values in the uniform
strain area when the external load value corresponds to the time strength limit.
And fig.5 shows the ratios of transverse strains.
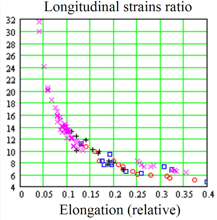 |
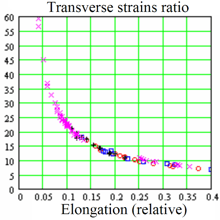 |
Fig.4. The ratio of average
longitudinal strains in the non-uniform strain area to the values in the
uniform strain area. |
Fig.5. The ratio of average transverse
strains in the non-uniform strain area to the values in the uniform strain
area. |
At the same time in local areas the strain values will already differ by
orders! Not only the experimental data but also the obtained by us functions of
local strains distribution across the specimen thickness indicate this (see
fig.6). And it means that the limiting state criteria, obtained in the course of
simple mechanical tests of the specimens, cannot reflect the limiting state of
the material and, particularly, the limiting state of the structural
element.
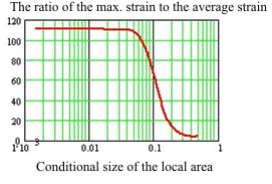
Fig.6. Dependence of the ratio of maximum
strain values in the local failure initiation area to the average strain on the
size of the local area.
But, in order to realize this, it is necessary to overcome the
well-established idea about the internal stresses and to remember that the
stresses - "sigmas", which we are all so much used to – are not stresses. This
is an external specific force applied to the specifically shaped specimen, which
changes the internal stresses. Thus, this is a conditional equivalent of
internal stresses!
"Conditional" - because the indispensable conditions are: the specific shape
of the specimen and the specific procedure of testing.
Only upon understanding the physics of the process of the material’s
resistance to straining it is possible to realize what the internal stresses are
and how and when they occur. Here the well-known from fracture mechanics concept
of a "structural element" - an elementary volume, in which the characteristic
changes of the material take place during its straining – is of great help.
Fig.7 shows sequentially, how the external specific force, while "splitting"
to components, influences the material, straining it in different directions
(glide, normal, width) and rotating it in the space, which causes occurrence of
the appropriate internal forces of the material’s resistance to straining and
which finally determines the input of the material’s proper energy for
resistance to the external load. It is obvious that the strains, which we can
measure (longitudinal and transverse), represent the algebraic sums of
projections of the internal physical strain vectors onto the usual for us
directions – along and across the applied force axis.
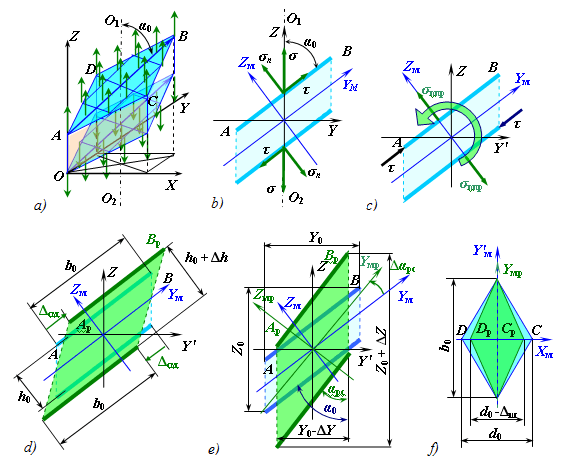
Fig.7. Structural element strain at uniaxial
tension.
Schematically the process of the material’s resistance to the external load
can be represented as follows (see fig.8). Any external exposure (from simple
uniaxial to the most complex one) of a specific object made from the
investigated material, including the specimen or a complex part, always "splits"
in the material to three force and three moment (rotational) components, except
for the uniaxial loading of a cylindrical specimen, when it "splits" to two
force and one moment component. The presented scheme shows that the internal
stresses – the difference of the internal energy density in the local and the
adjacent to it areas - represent the difference of potentials.
Moreover, now we can say that internal stresses - are a special
unified energy characteristic of the material’s equilibrium state, which is
determined (see fig.8) by the set of physical strain-force parameters reflecting
various types of the internal energy variation as a result of various types of
exposure of the specifically shaped material.
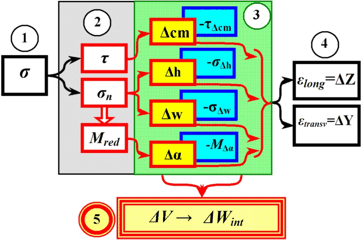
Fig.8. The material’s reaction to external
force exposure: 1 - external specific force; 2 - force components of external
exposure inside the material; 3 - an aggregate of local strains and material’s
resistance – parameters of internal stresses; 4 - external characteristics of
the material’s reaction; 5 - internal stresses - variations of internal energy
density.
Expressly for "gourmets" the following definitions of the material’s state
can be offered. Any material possessed a proper internal energy characterized by
the average energy density, which could be represented by the two zero-rank
tensors - scalar and vector potentials. The energy distribution in the volume of
even "isotropic" material is non-uniform. But it is characterized by the strict
order along each of the possible, quite definite directions of variation of the
initial energy value - by the three linear (ordinary) vectors (the first-rank
tensors) and one axial (rotational) vector. All these - are individual qualities
or properties of the material, determined by one characteristic - the average
energy density, which depends neither on the object’s shape nor on the nature of
the external exposure. But at the same time the "quite definite" linear
directions of variation of the initial energy value - normal, shear and width,
determined by the glide plane position in the force or another external field
space - already depend on the shape of the object made of the investigated
material.
While resisting to the external exposure, the material uses its proper
energy. The input of this energy can be evaluated by the work of the external
field - the strain-force parameters expressed by two complete second-rank
tensors (force and strain), or by two pairs of linear (symmetrical) and
rotational (antisymmetric) tensors. It should be noted that the loss of an
antisymmetric rotational tensor in the theory of materials’ resistance led to
the deeply wrong idea about the existence of "principal stresses" and "principal
strains". It is impossible either theoretically (in case no mistake is made) or
in real conditions to find such a "plane", where there will be no shear forces
and angular moments! It is simpler to understand it physically: the material’s
energy consists of the two, practically equal by quantity components - potential
(electrostatic), determining the "repulsion" of atoms, and quantum, determining
the "attraction" of atoms. And it follows that during any impact on the material
in any of its areas both fields - quantum (attraction) and potential (repulsion)
- always "work". So, the pair of antisymmetric tensors, lost by the theory of
materials’ resistance, exactly describes the input of the quantum component of
the material’s internal energy for resistance to the external exposure. And, as
a matter of fact, what would remain from the material if the forces, attracting
atoms to each other, were really cast away?!
The obtained by us investigation results allow "seeing" how the material
resists the external exposure.
Variations of the internal forces of the material’s resistance in the
non-uniform specimen strain area to the external tensile force are shown in
fig.9, where for the sake of comparison the graph of the external specific force
variation is presented.
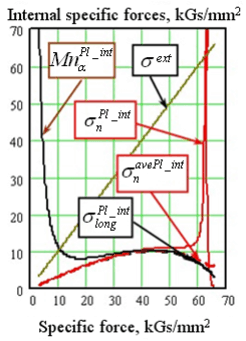
Fig.9. Dependence of internal forces of
resistance to elastic and plastic strains St.6 on the specific force in the
non-uniform strain area: σext - stresses due to the specific force of
the external load; σlongPl_int - the graph of stresses due
to the normal longitudinal plastic (mechanical) strain;
σnPl_int - the graph of stresses due to the normal
longitudinal plastic (physical) strain; σnavePl_int - the
graph of variation of the average across the specimen value of the internal
force of resistance to the longitudinal strain; МnαPl_int - the moment of resistance to plastic variation of the glide angle.
As it is seen, the force physical characteristics of the material’s
resistance to straining depend on the external specific force, which is taken
for internal stresses. Their appearance is not simple and they are far from
being proportional to it! Moreover, the special or critical points, which can be
seen on the graphs, can hardly be linked with the yield strength or the time
strength limit.
If we return to the latest ideas of the classical fracture mechanics about
the process of failure development, formed by the 80-s of the XXth century and based on various experimental and theoretical investigations, it can
be seen that, "to put it mildly", they do not rely on the well-known mechanical
characteristics of materials either (though in absence of anything else, they
are used in calculations).
It should be noted that the most terrible consequence of the established
mistake in realizing of the internal stress physics, one might say, the
craftiness of the mistake shows itself only now, when the problem of the
material’s state and efficiency determination - an important component of the
problem of complex technical objects’ residual life assessment - has become so
urgent.
The danger consists in the fact that the mechanical characteristics obtained
in the course of the specimens testing – the reference limiting values of the
specimens strains and specific forces – the conditional equivalents of internal
stresses, are considered to be proper characteristics of the material,
determining its resistance to any external loads independently from the shape of
the product made of this material. This was the source of the principal mistake
being peculiar to all methods of internal stress "measurement" without
exception.
Thus, the obtained by us results of experimental and theoretical
investigations allows "materializing" the conclusions, which the fracture
mechanics approached practically in real earnest long ago, as well as presenting
the limiting states and the inseparably linked with them background concepts, as
follows:
-
the limiting state of the material - is the minimum possible density of the
internal energy – a limiting potential determined only by the value of the
average density of the internal energy, being an individual quality of the
material. It depends neither on the dimensions of the structural element nor
on its loading conditions;
-
the limiting state of the structural element is determined by the ratio of
the dimensions of the local are, in which the material reached the limiting
state, as well as by the dimensions of the structural element’s area, in which
this local area is located;
-
the local area dimensions are determined by the material’s individual
qualities, the structural element’s dimensions and its loading conditions and,
in turn, they determine the nature of the actual distribution of local strain
in the structural element’s volume;
-
the actual state of the material in the local area - the value of the
actual density of the internal energy - is an actual potential determined by
the individual qualities of the material, the location site of the
investigated area in the structural element’s volume and by its loading
conditions;
-
the internal stresses - the difference of potentials - is the difference of
the internal energy density in the local and the adjacent to it
areas.
As it can be seen, the commonly known values of the limiting states - yield
and time strength, obtained in the course of simple mechanical testing of the
specimens, cannot reflect the limiting state of the material and, particularly,
the limiting state of a structural element.
Thus, the investigation results analysis brings us to the known from the
fracture mechanics conclusion that we should already speak about several
different criteria of failure: the limiting value of normal strain at uniaxial
tension, the limiting value of strain by width at uniaxial compression and the
limiting value of shear strain at torsion or bending, as well as various
combinations of the limiting values at complex loading.
All this requires more attentive approach to the diagnostics of the
material’s stress-strain state and to the procedure of assessment of the degree
of the material’s actual state closeness in the structural element’s local area
to the limiting state, both for the material and for the entire structural
element, because now it is clear that these are far from being the same!
It is quite obvious that prediction of possible periods of safe
operation of real "ageing" structural elements (the main type of damages
development) based on the results of the material’s SSS diagnostics using
calibration dependences, obtained in the course of simple mechanical testing of
specimens without evaluation of a fatigue failure development time and rate in a
specific object and under specific conditions, is not simply useless but
extremely dangerous!
The point is that all the known methods react to elastic strains. And in a
real structure elastic strains never exceed the values, which correspond to the
yield strength.
Moreover, taking into account the acute (from units to several tens of
micrometers) locality of the fatigue damaging development process, the
peculiarities of the local physical strains distribution and their ratios with
average values of strains, one might state that, using conventional active
methods of diagnostics, possessing the large averaging base (10 mm at best),
most probably, we shall not simply detect the damaging development area, not to
mention the possibility of the developing damaging parameters determination.
The obtained results of investigation of the rules of the physical strains
distribution directly indicate the necessity of development of the new normative
documentation, which would regulate certification of means for structural
materials’ stress-strain state diagnostics, as well as the techniques for
"adjustment" of means for SSS diagnostics.
We used the term "adjustment" instead of the more usual term "calibration",
because we wanted to stress that the obtained by us results of experimental and
theoretical investigations make it possible to carry out the diagnostics without
the preliminary testing of the specimens, the shape of which is most often
selected based on the conditions of convenience of the diagnostic means’ sensors
installation. And, as a rule, it does not comply with the standard for
performing of mechanical tests.
Thus, the new State Standard of the Russian Federation GOST R 52330-2005
"Non-destructive testing. Stress-strain state test on industrial objects and
transport. General requirements", which was put in effect in 2005, is the first
little but, perhaps, the most difficult and important step on the way of turning
of structural materials’ SSS diagnostic methods and means from the spectacular
but self-sufficient (and therefore useless) field of diagnostics into an
effective - really necessary and useful - tool for actual state assessment of
structural materials and structures. |